Cover Glass Design & Integration Service
If your industrial LCD display faces rough environmental conditions, your LCD design must prioritize coverglass protection and ruggedization. Not only does a coverglass provide resistance to scratches and abrasions, it increases optical clarity and support touchscreen functionality. AGDisplays offers a variety of coverglass substrates for upgrade or replacement. With varying characteristics between our coverglass options, we help you choose the best option based on your application need.
Replacing your LCD coverglass with AGDisplay provides you an opportunity to selectively enhance LCD protection, clarity and more, without breaking the budget. We use name brand materials with low MOQs and competitive pricing so we can help meet all your project goals. Optimize your coverglass repair with various optical coatings to increase protection, minimize reflection and refraction, and offer surface finishes ideal to your application.
To install the coverglass, we use LCD bonding as our primary means of integration. LCD bonding is one of various adhesive options available on the market and it offers a wide range of benefits. Bonding can prevent coverglass shattering, add protection from water/dirt and increase optical clarity.
AGDisplays gives you access to fully equipped supplier resources who are able to meet customizable appearance and specification requirements to fit your LCD project. Our coverglass offerings are paired with value added optical coatings and bonding integration methods to secure LCD components and designs for overall ruggedization and extended lifespan.
Get A Quote
Value Added Options
Take your cover glass integration one step further by adding a touch sensor to your design. If your LCD does not already have touch screen capability, AGDisplays offers virtually limitless touch sensor options for integration with your cover glass. Quickly upgrade your LCD monitor to an up-to-date touch screen that is fast, intuitive and productive. Learn more about touchscreen integration here.
In the future, when your coverglass has been worn from normal wear & tear, you will only need a simple change of the top film for a clean and polished finish. With a restoration of the coverglass and top film coating, your coverglass will be restored to new. Read more about our film enhancements here.
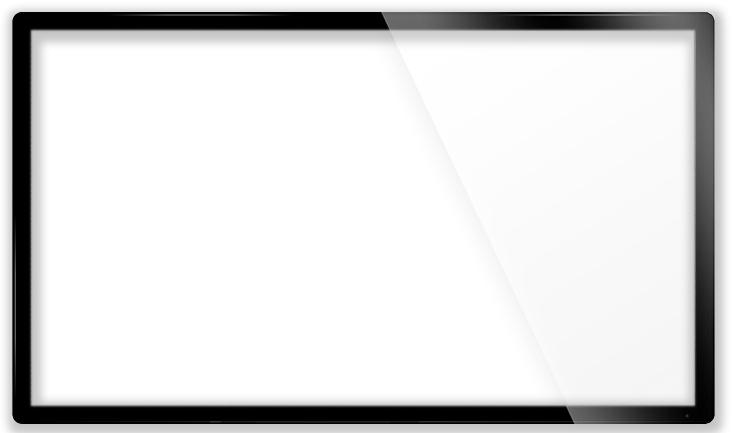
Cover Glass Benefits
Why would someone need to add a cover glass to the front of their LCD? Stock coverglass material does not hold up well against scratches or damages, leaving your LCD with large vulnerabilities. To protect your LCD display, you will need to install a superior cover glass or other strengthened polycarbonate material to the LCD for protection.
Display assemblies including (or integrating) a strengthened cover glass substrate has become a popular solution in years past, as the trend for reducing the thickness of mobile and LCD devices has been on the rise. Utilizing a glass substrate has the superior advantage of increased hardness and scratch resistance as well as having a higher design value. Pairing glass with various strengthening methods increases the robustness even more. There are many ways to increase glass strength. A popular approach is chemical strengthening. where a compressive surface layer is formed via a high-temperature ion-exchange process when sodium ions are replaced by larger volume ions such as potassium.1 This process may differ from manufacturer to manufacturer. AGDisplays offers a variety of cover glass substrate options to add durability and protection to an LCD. From our wide selection of glass, each material substrate provides unique benefits.
AGDisplays employs an integration method commonly known as LCD bonding. LCD bonding uses one of various adhesive options available on the market for a wide range of benefits. In this case, integrating a cover glass to the LCD requires a h2 adhesive bond to fuse two LCD components together to form one unit. Typically, the cover glass is bonded straight to the LCD unit itself. AGDisplays offers three different bond integration methods: optical bond, OCA bond, and tape bond. Each of these services contributes unique benefits to an LCD design; however, every design specification and requirements are different. Selecting the wrong bonding method for your design may have adverse effects on design quality. That’s why your design is in the hands of an AGDisplays expert, we know the unique aspects of bonding, and are able to select and integrate services to designs that will benefit your overall specifications.
Benefits:
- Cover glass is enhanced and treated for strength
- Cover glass is used in LCD and touch screen applications from industrial to commercial
- Add an optical coating onto the cover glass for more optical features. Quality cover glass coatings influences and controls transmittance, resistance, absorbance and reflectance
- Customizable screen printing for a polished and professional look to your LCD
- Three bonding methods available: optical bond, tape bond, OCA bond
- Bond a touch sensor with your cover glass
State of the Art Equipment:
- Class 1000+ Clean Rooms
- CNC Machines
- OCA Bonding Capabilities
- PCB Design Software
- Programmable Automated Test Equipment
Cover Glass Features*:
- Chemically-Strengthened
- Scratch and Crack Resistant
- Improved Surface Quality
- Enhanced Response
- Thin and Light without Fragility
- Promote Sunlight Readability
- Ruggedized
- Protection From EMI Interference
Cover Glass Options
Chemically-strengthened soda lime is used for thin, rugged displays. It can be strengthened from 8 to 16 hours, depending on application. Chemical strengthening is ideal for soda lime sheets under 3 mm. If ruptured, soda lime will simply crack rather than shatter. AGDisplays offers a variety of different soda lime options: clear & tinted; low iron; anti-glare; heat absorbing float glass and more.
Clear and tinted: this option offers a high light transmission with the option to add AR coating for extra transmission; this material is eligible for chemical strengthening and features good flatness with no green tint.
Moh’s Scale Hardness |
5 to 6 |
Refractive Index (sodium D line) 1 µm 2 µm |
1.5231.5111.499 |
Thickness Availability |
0.55 mm to 25.4 mm (0.02” to 1”) |
Grey glass: this glass is tined and is used for restricting or reducing light transmission. Benefits include increased privacy; reduce glare and has a reduced opacity.
Transmission Ranges |
62% (lightest grey) 57% 31% 14% 9% 8% (darkest grey, nearly black) |
Thickness Availability |
3 mm to 6 mm (.125” to .234375”) |
Low iron soda-lime: this option offers a high light transmission with the option to add AR coating for extra transmission; this material is eligible for chemical strengthening and features good flatness with no green tint.
Moh’s Scale Hardness |
5 to 6 |
Refractive Index (sodium D line) 1 µm 2 µm |
1.523 1.511 1.499 |
Anti-glare reducing etched soda-lime: this glass offers glare reduction with a high resolution, superior durability and anti-Newton ring.
Gloss |
60-130 (US Gloss, measured at 60° by a BYK Gardner Glossmeter model 4501) |
Thickness Availability |
60-130 (US Gloss, measured at 60° by a BYK Gardner Glossmeter model 4501) 0.7 mm to 4.75 mm |
Low Emissivity (low E): this glass provides a higher window U-Value, increased insulation performance, energy savings, and decreases color fade by blocking UV light.
Visible Light Transmission |
76% |
Thickness Availability |
3.2 mm, 5.0 mm |
Heat absorbing float glass: this glass features IR absorption.
Refractive Index at sodium D Line (ND) |
1.5184 |
Thickness Availability |
3.175 mm & 6.35 mm (.125” & .25”) |
AGC Dragontrail™ is a chemically strengthened and tempered float-glass material that is 6x more durable than soda lime glass. With this strength, the glass can be produced in thinner material. This material does not contain harmful materials like arsenic, lead or antimony.
Vicker’s Hardness Unstrengthened Strengthened |
596 kg f/mm² 673 kg f/mm² |
Refractive Index at sodium D Line (ND)Thickness Availability Standard Special Request (MOQ req.) |
0.8 to 1.1 mm 0.5 to 5.0 mm |
Refractive Index |
1.51 Nd |
Damage and Scratch Resistant |
>600 MPa strength 35 < depth of layer (DOL) < 45 µm |
Corning® Gorilla® Glass is a thin sheet glass with a high degree of chemical strengthening. Benefits of Gorilla® Glass include high scratch resistance, high retained strength after use, and pristine surface quality.
Unstrengthened Strengthened |
534 kg f/mm² 649 kg f/mm² |
Thickness Availability |
0.4 mm to 2.0 mm |
Improved Damage Resistance |
≥ 950 MPa @ 40 µm DOL, compressive strength |
Refractive Index Core Glass Compression Layer Photo-Elastic Constant |
≥590 nm 1.5 1.51 31.9 nm/cm/MPa |
Optical Coatings
One issue that may arise from the normal or enhanced front of screen structure is reflection, caused by the multiple layers in an LCD stack. To properly optimize cover glass and other enhanced elements in an LCD design, AGDisplays incorporates (optional) optical coatings to the LCD, such as anti-glare, anti-reflective, and/or other surface treatments. Light reflections cause a distracting flare for the LCD and contributes to overall image quality. These treatments are placed on the front surface of the display, creating different reflection patterns to reduce the negative readability reduction and to enhance optical properties. Mostly, these coatings are thin-film layers that cause a disruption in light wave patterns. These coatings are applied to glass and other substrates. These can be added by vacuum evaporation methods or low-cost wet-coating processes. Features below are dependent on solution selection.
Optical Coating Features:
- High Transmittance
- Low Reflectance
- Durability
- Scratch and abrasion Resistance
- Contamination and Weather Resistant
- Easy to Clean
- Electro-Magnetic Shielding
- Oil and Fingerprint Resistant
Optical Coating Selection
Anti-Reflective (AR) treatment reduces ghost images, which are often produced in builds that have multiple reflective surfaces. Integration of this film optimizes the readability of a display. The film handles both internal and external light sources of an LCD. This means ambient light, and light reflection within the display are reflected in order to increase display readability for the user. AR films come in many thicknesses, varying the amount of destructive interference the film has on reflection. This treatment features high transmittance, low reflectance, durability and an easy-to-clean surface. AR coating as a surface treatment is best suited for medical displays.
Anti-Glare (AG) reduces glare on a screen to increase readability and reduces fingerprints and smudges. The main difference between anti-glare technology and anti-reflective technology is that AG deal with external sources of light that bounce off the surface of the LCD, such as sunlight or ambient light. The AG coating is a rough, textured coating, created to diffuse reflective light. There is a trade off when using this film; the AG properties reduce glare efficiently but degrade light transmission properties. However, choosing the right type of AG for your application will yield positive results significant to your project, while keeping degradation at unquantifiable levels.
Oleophobic/hydrophobic in an oil repellant coating that resists dirt, water, grease and oil to prolong and enhance glass performance. This film works by repelling grease and preventing it from sticking to the glass surface. An added feature to this coating is that it is resistant to severe abrasions and scratches due to the oleophobic layer being more slick, reducing friction. Overall, this allows surfaces to be easy-to-clean, and repeated removal of fingerprints all while maintaining pristine image quality, even after repeated cleaning. Unfortunately, this layer has a lifespan; however, it can be prolonged by handling the layer with care. Here are some tips for keeping a lasting oleophobic display:
- Do not use alcohol-based solvents or household cleaners on the display
- Use a clean cloth and a small amount of water to clear away smudges and fingerprints
- Add another layer of screen protection
Transparent conductive coatings are used in electro-magnetic shielding and electrical heating display applications. These coatings allow for low reflectance but are specific in their applications. The coating features high visible transmission and excellent infrared reflection. Two commonly used conductive coating solutions to combat EMI interference are indium tin oxide (ITO) films or wire mesh solutions. EMI shielding effectiveness generally will correspond with the amount of coating resistance in the particular film solution being used. Most conductive coatings are 30 ohms/sq or below. Fine wire mesh can be conductively plated, increasing shielding effectiveness, with surface resistance numbers close to 0.1 ohms/sq, allowing for a much better shielding effectiveness. Consult an AGD expert for more information.
References
1S. Gomez, et al., "Designing Strong Glass for Mobile Devices." SID Symposium Digest 47, paper 69.2, 1045 (2009)