FAA Part 145 Repair Station
The Federal Aviation Administration has found AGDisplays in compliance with the requirements of the Code of Federal Regulations Title 14 Part 145 for Repair Stations. AGDisplays employs a Part 145 Limited Airframe, Limited Accessories rating.
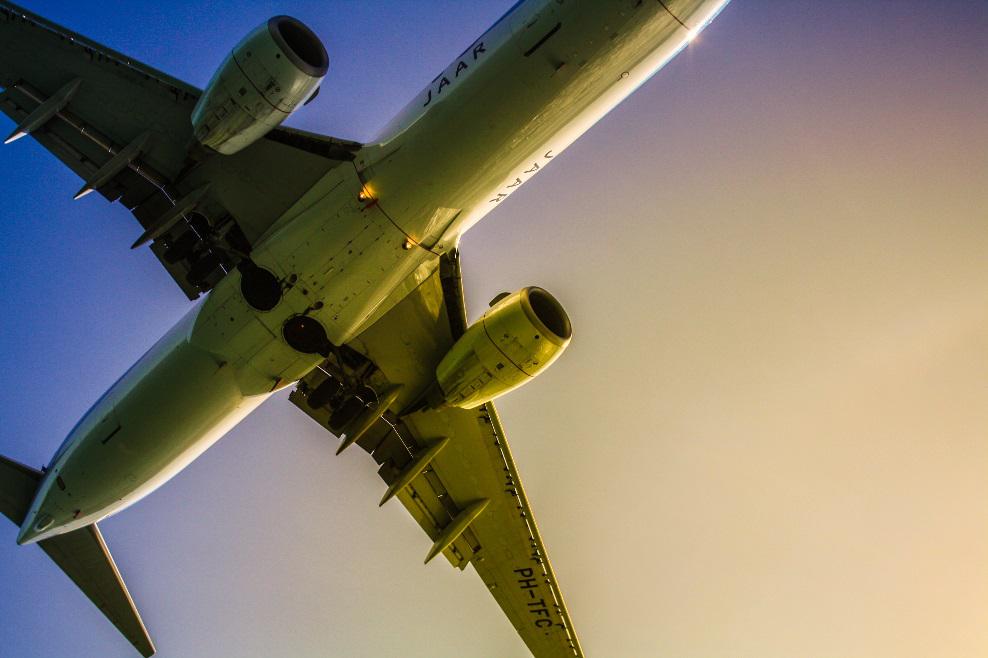
Replacing in-flight entertainment TFT-LCDs costs companies thousands of dollars. Even the smallest blemish or scratch can prompt an LCD replacement. AGDisplays corrects scratches by providing top and bottom glass polarizer repair for in-flight entertainment LCDs. With AGDisplays’ services, you can bypass the expensive LCD unit replacement and take advantage of our TFT-LCD repairs. Repairing instead of replacing decreases extra expenses and increases panel longevity.
A polarizer is a thin film on the top or bottom surface of the TFT-LCD that can be replaced using AGDisplays’ approved process specifications. Our experts perform LCD repolarization in one of the multiple Class 1000 clean rooms that are located in our facility. Using a clean room is important because it minimizes the risk of contamination find its way into the LCD as an AGDisplays technician is performing a repolarization on an LCD display.
AGDisplays services have expedited forecasts, based on quantity of order and material. LCDs can be re-polarized to return your scratched display to original form. We also boast a minimum fallout rate, so you know our repolarization processes are efficient. We achieve low percentages by training technicians to no less than an exceptional standard.
AGDisplays maintains a technical library with OEM specifications, traceability documents and other technical information.The repair station properly documents, controls and stores all applicable paperwork accompanying services performed on articles for return to service.All repair station personnel are required to be thoroughly familiar with the requirements of the repair station manual and all applicable FAA regulations. Our repair station personnel must follow the repair station quality control system when performing maintenance on articles being returned to service.Our FAA Part 145 Repair Station performs multiple inspections throughout the various stages of the maintenance process.
AGDisplays employs the ATOM system for documentation reliability, traceability and performance accuracy throughout the inspection and maintenance stages. The ATOM system is used for the work order lifecycle documenting system which includes preliminary, hidden damage, incoming data, repair results, outgoing data inspection, rework, discrepancies and return to service inspections.
A preliminary inspection involves a visual inspection performed by a Technician. The in-process inspection is an inspection performed during maintenance of an article to ensure that further steps wouldn’t compromise the completion of the repair.If it is suspected or known that the article was involved in an accident, prior to servicing the component or article, it will be subjected to a hidden damage inspection. Hidden damage inspection can be initiated by the customer, or when shipping damage is detected or suspected during preliminary inspection.
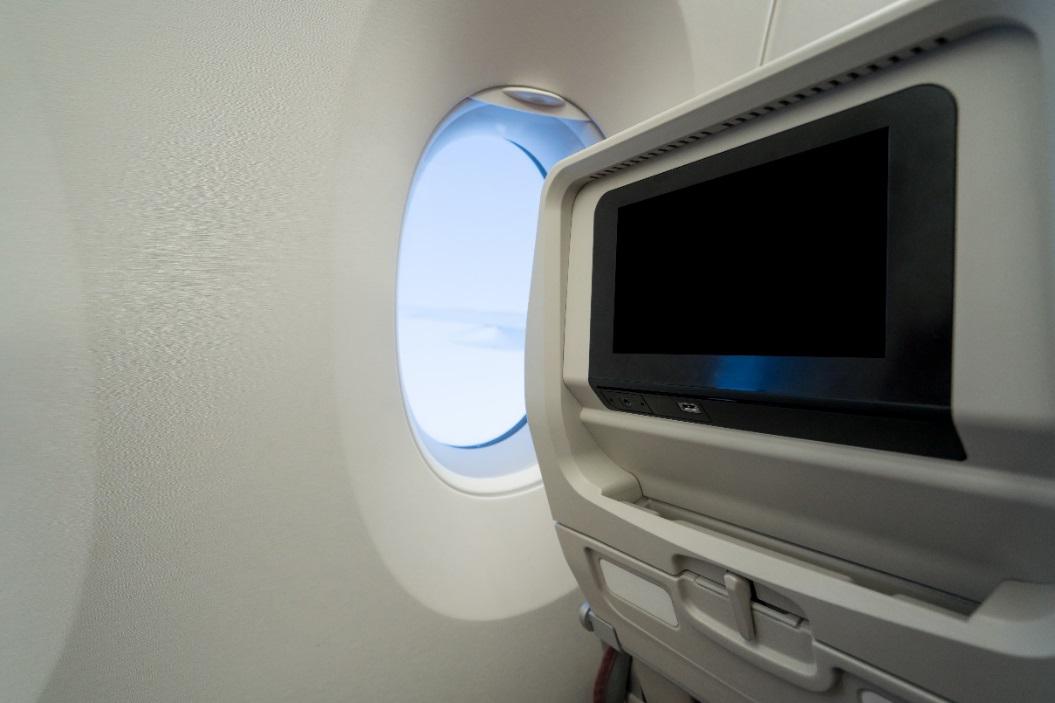
The raw materials inspection process is used to ensure the quality and protection of products moving in and out of the repair station facility.Lastly, the final inspection ensures proper inspection on a completed article and to ensure its paperwork and lifecycle records are complete and accurate prior to authorization of return to service.In our final quality control testing, we authenticate and record workmanship and data functionality on all LCDs leaving AGDisplays’ facility.
The AGDisplays facility performs maintenance and repairs to in-flight LCD panels in our facility in accordance with contract requirements. We employ Part 65 certified repairmen trained to inspect, repair, and approve airworthy LCD panels within the Repair Station's rating. Each Repair Station position in the repair station is evaluated on a regular basis to determine that the position is in compliance with CFR parts 43, 65, 91, and 145.Employees are subject to initial, recurrent and specialized training for the benefit of quality, safety and standards. Recurrent Training will be provided to support, refresh and/or expand existing knowledge and skills employees obtained when first hired. Specialized Training will be provided to employees as required;additional training necessities will be determined during a position requirement review.
With our Air Agency certificate, AGDisplays ensures that programs, quality systems and methods of compliance are stringently reviewed, evaluated, and documented when it comes to the maintenance of FAA-approved articles. Companies looking for in-flight panel repairs can now contact AGDisplays to discuss capabilities and how we can serve you. Our dedicated teams are committed to becoming your trusted partner. AGDisplays is in the process of expanding our in-flight LCD repair capabilities.