Industrial Repair Service
Industrial repair utilizes all facets of AGDisplays’ capabilities. We repair most aspects of LCD technologies so that our customers do not have to replace whole units for minor repairs. AGDisplays are experts in LCD panels and LCD technology. At our 84,000 square foot facility, AGDisplays performs both low-volume and high-volume production levels; we maintain high tech, state of the art equipment to perform precise procedures. With our high level of expertise, our teams provide technical skills and lend our creative problem-solving abilities to give our customers LCD displays that meet the demanding needs of your industries.
- Multiple state-of-the-art Class 1,000+ clean rooms with integrated assembly lines
- Team with 40+ years of Technician and Repair Experience
- Two Oven Chambers
- Environmental Test Chamber
- Five Lines of OCA Equipment
- ESD Controlled Production Floor
- Radiometer/Photometer
- Laminating Equipment
- LCD De-laminating Equipment
- Universal LCD Test Equipment
With over 40+ years of experience, we train our individuals through a specific curriculum in which we evaluate regularly. Our team is ready to deliver high-performance display repairs to our customers. Trained personnel are evaluated prior to employment and during employment on a regular basis to determine their workmanship quality exceeds the standards set by AGDisplays. We also provide repair warranty services for panels that are no longer under OEM warranty.
AGDisplays is focused on refurbishing and repairing your LCDs; we specialize in providing cost-effective alternatives to LCD replacements. We may use recycled LCD parts, which are always 100% tested. Using refurbished parts gives the customer the ability to keep cost low. Using AGDisplays’ repair/refurbish service guarantees your products are using quality and inspected components.
AGDisplays most often uses brand new, quality LCD components when repairing and refurbishing your display product. Our company values quality components, that’s why strictly maintain our databases, and follow supply chain processes. We have an International Procurement Office in China that are constantly verifying vendors with whom we maintain current business practices.
Our LCD experts prepare custom display layouts including unit dimensions and segment content to redesign your panel for optimal functionality. Inspections on deliverables are evaluated to ensure AGDisplays is only working with quality materials. During manufacturing, various product inspections take place such as performance measures. For quality assurance measures, we perform a full diagnostic analysis for each repaired unit that can include the following:
- chromaticity analysis (color temperature)
- luminance analysis
- polarizer absorption axis analysis
- optical film stack analysis
- pixel defect inspection
- uniformity analysis
Customer Benefits
- Our quality resources become available to you at an affordable price. We have a direct relationship with LCD distributors, providing our customers with the same resources.
- Extend the life of your product, keep maintenance costs down and work efficiently
- Utilize our access to End of Life (EOL) panels that may be out of reach for others
- Warranty program for products no longer under OEM warranty
- Standard repair pricing structure
What is LCD repolarization?
LCD repolarization is the process in which a person or company will remove an existing polarized film from an LCD stack up. Polarizing films are used in an LCD stack up to increase readability and clarity created on the LCD. The films polarize light to create a defined direction. LCDs may use various types and combinations of films; not all of these films are considered polarizing films. In the LCD Industry typical laminations can consist of optical polarizer laminations to the LCD glass surface or perhaps an anti-reflective film laminated to the top polarizer. AGDisplays employs three different types of polarizers: reflective, transflective or transmissive. An LCD stack configuration is determined by the lighting conditions your LCD will operate in.
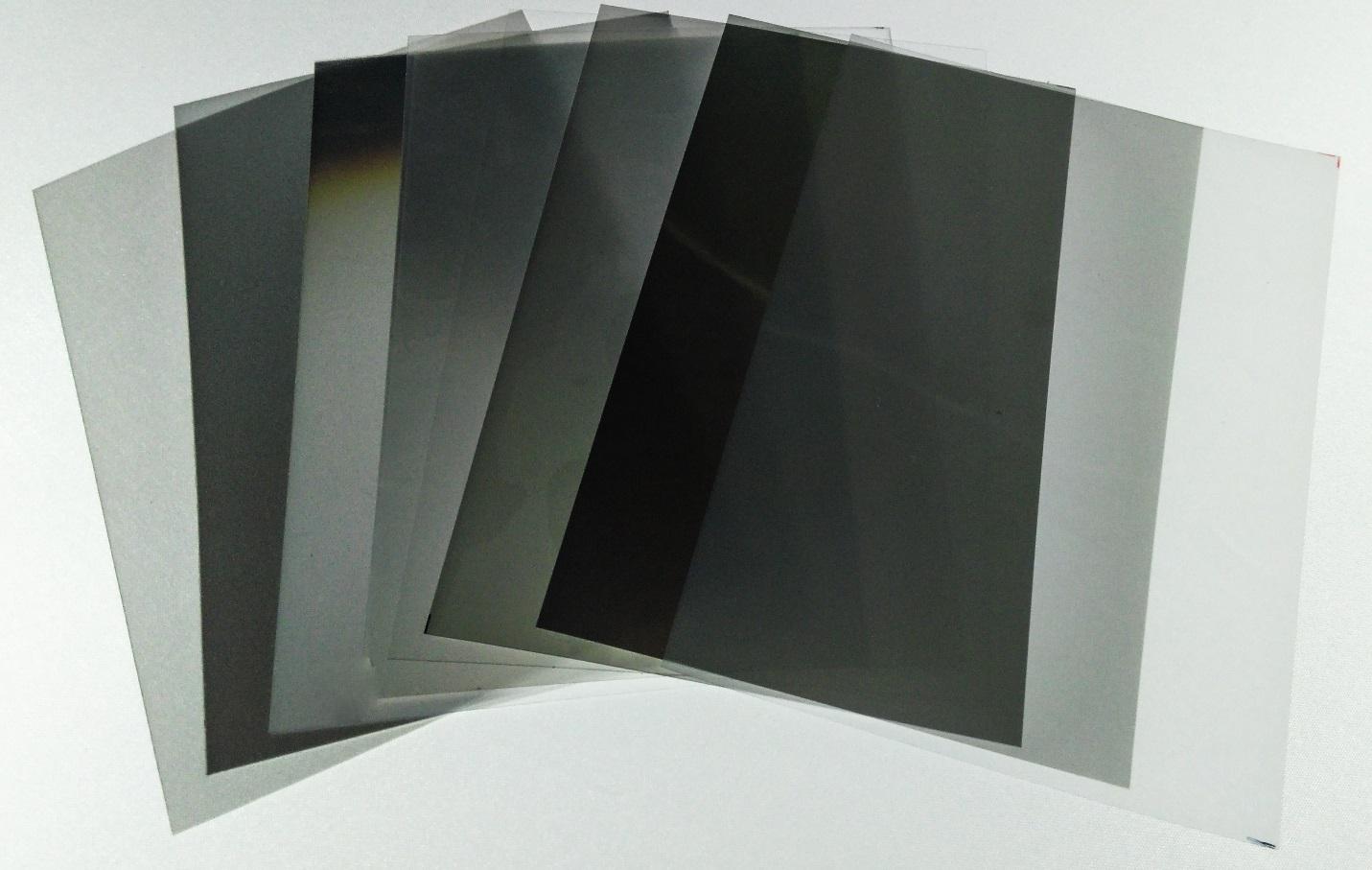
Reflective polarizers are applied to the bottom layer of the LCD glass and reflect 100% of the ambient light that enters through the top layer of the glass. Transmissive polarizers allow the light from a backlight source to pass through the bottom and top layers, towards the user. In this instance, the backlight must be on for the display to be readable. Benefits of this polarizer are increased display brightness, reduced driving current and extended half-life of the backlight. Transflective polarizers allow display readability with the LCD backlight on or off. This polarizer reflects some ambient light passing through the front glass; at the same time, it uses the backlight source to pass through the glass.
The AGDisplays experts perform LCD repolarization in one of the multiple Class 1000 clean rooms that are located in our facility. Using a clean room is important because it minimizes the risk of contamination find its way into the LCD as an AGDisplays technician is performing a repolarization on an LCD display.
Depending on the type of polarization used in the particular LCD build, the film may also increase display contrast and readability, create sharper and clearer image quality, provide deeper colors, increase viewing angles and more.
LCDs can be repolarized to return your scratched display to original form, and additional lamination services such as anti-reflective and anti-microbial properties, EMI protection, and LCD protection. With our lamination enhancements, you can be assured that your LCD is protected from surface scratches, acid-etching, and other particle contaminants. Replacing a polarized film will not repair damage to a broken LCD. AGDisplays can replace damaged LCD screens that cannot be repaired by repolarization.
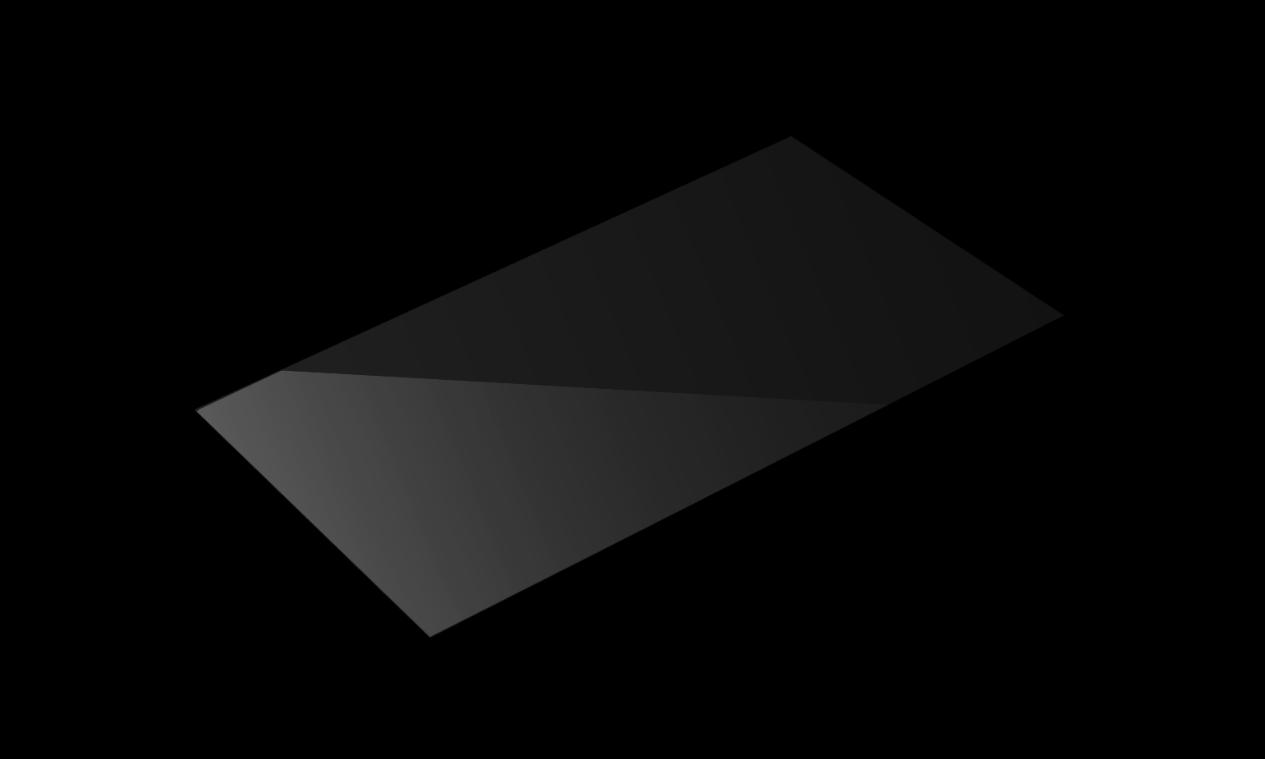
What is an ESD Flooring System?
An ESD Flooring system is used to discharge electrical static charge. The discharge of the electrical static helps reduce or eliminate the possibility of damaging sensitive electronic components during the manufacturing process. Even the smallest ESD discharge may have an adverse effect on electronic components. Using a ESD flooring system limits component failure as part of AGDisplays’ quality control processes.
An ESD-control floor coating has conductive particles within it which allows the coating to be electrically active; this allows electrical current to travel through it—permitting the electrical charge to travel from one point to another. This flooring works together with ESD protection devices like footwear, garments, and grounding straps, to minimize body voltage generation (BVG) and to control grounded discharge.
What is a class 1000/10,000 clean room?
Cleanrooms are used across any industry where small contamination particles would negatively affect product manufacturing processes. A cleanroom is a controlled environment that is designed to keep a low level of air pollutants such as dust, airborne microbes, chemical vapors and more. Other parameters that are controlled include temperature, humidity and pressure. An air filter, called the High Efficiency Particulate Air (HEPA) filter, is designed to trap particles that are 0.3 micron and larger from getting into the controlled environment. In other more stringent requirements, clean rooms may use an Ultra Low Particulate Air (ULPA) filter. Employees who work in cleanrooms train in contamination control theory. Employees enter and exit cleanrooms through airlocks and/or gowning rooms. Employees are required to wear gowns made of material designed to trap contaminants that are naturally generated by the skin and body.
ISO 14644-1 Cleanroom Standards
Class | Maximum particles/m3 | FED STD 209E equivalent | |||||
>=0.1 µm | >=0.2 µm | >=0.3 µm | >=0.5 µm | >=1 µm | >=5 µm | ||
ISO 1 | 10 | 2 | |||||
ISO 2 | 100 | 24 | 10 | 4 | |||
ISO 3 | 1,000 | 237 | 102 | 35 | 8 | Class 1 | |
ISO 4 | 10,000 | 2,370 | 1,020 | 352 | 83 | Class 10 | |
ISO 5 | 100,000 | 23,700 | 10,200 | 3,520 | 832 | 29 | Class 100 |
ISO 6 | 1,000,000 | 237,000 | 102,000 | 35,200 | 8,320 | 293 | Class 1,000 |
ISO 7 | 352,000 | 83,200 | 2,930 | Class 10,000 | |||
ISO 8 | 3,520,000 | 832,000 | 29,300 | Class 100,000 | |||
ISO 9 | 35,200,000 | 8,320,000 | 293,000 | Room Air |
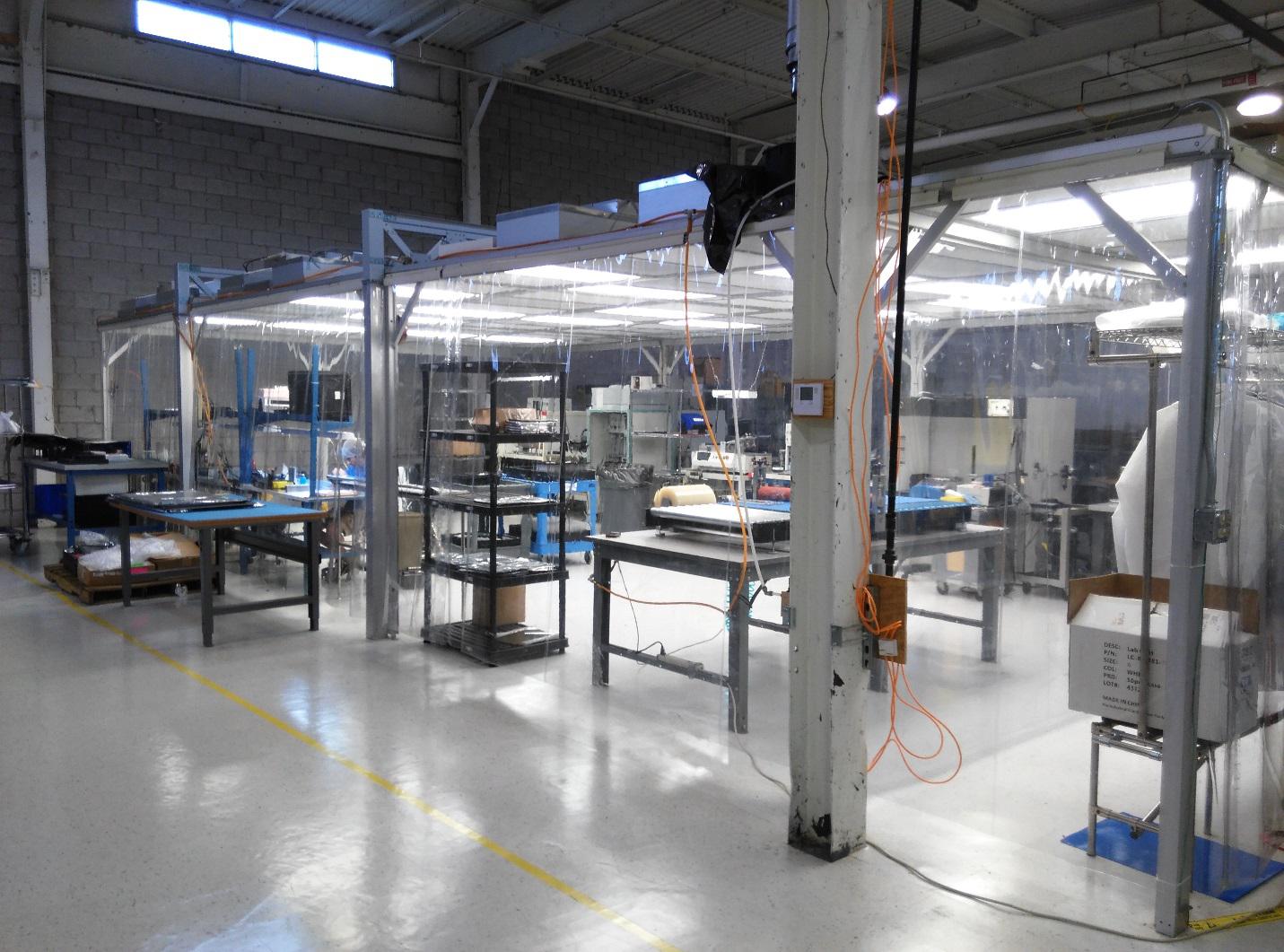