Lifecycle Support
Product lifecycle management is the process of taking your product from inception, to design, to manufacturing, to repair/service and then finally to disposal. Implementing an organized product lifecycle management program may be a challenge for companies who run into design and engineering challenges. AGDisplays works together with your teams to support your product’s life from the conception to disposal. At the end of a product’s lifecycle, we can provide EOL display and component alternatives to extend your product’s lifespan.
Centralizing the creation and management of all data and technology is fundamental to the success of a lifecycle management system. Below is an example of a simple engineering workflow. What follows is an in depth explanation of each stage and how AGDisplays supports your team every step of the way. These points may be modified or redirected due to a company’s system or the product itself:
Conceive
- Specification
- Concept design
Design
- Detailed design
- Validation and analysis (simulation)
- Tool design
Realize
- Plan manufacturing
- Manufacture
- Build/Assemble
- Test and quality control
Service
- Sell and deliver
- Use
- Maintain and support
- Dispose
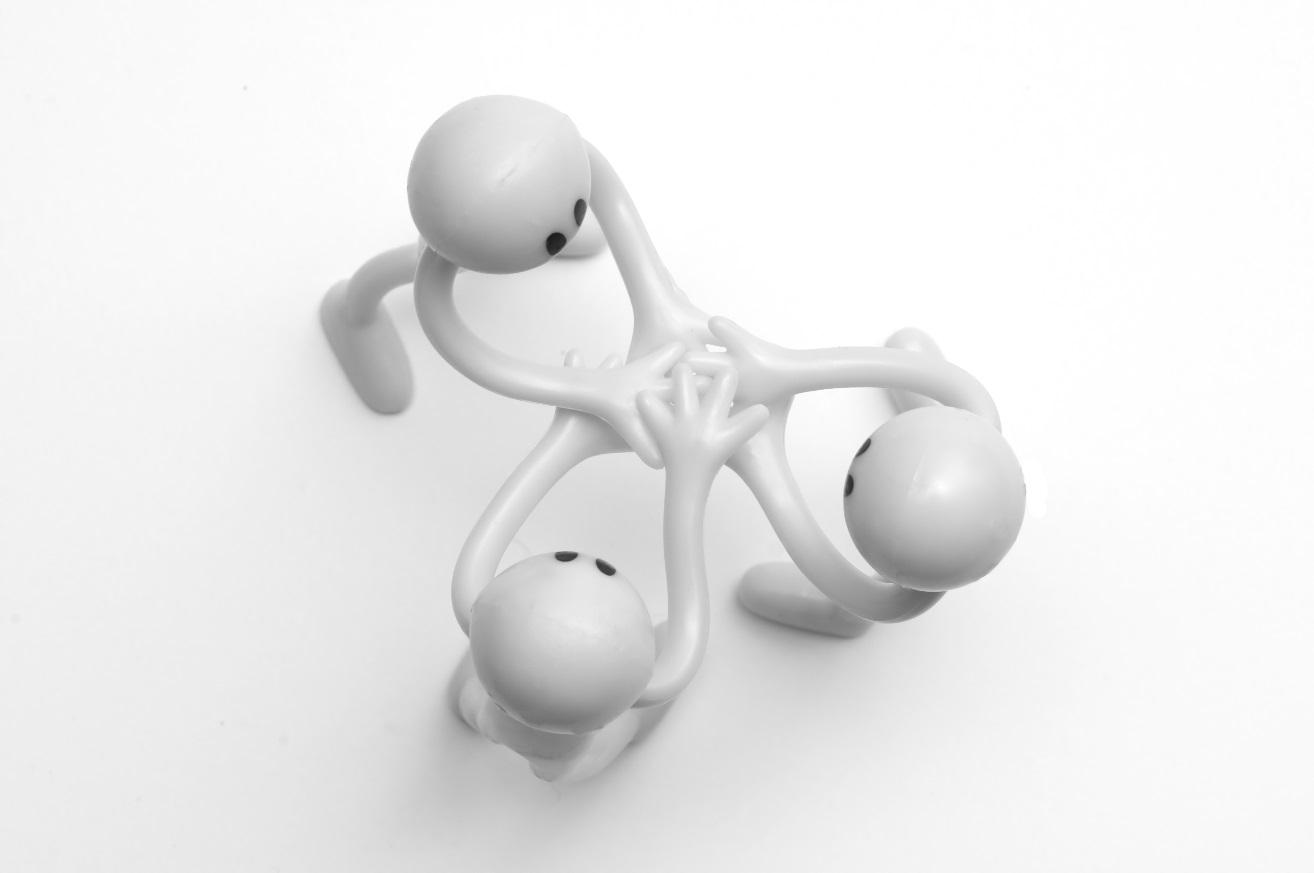
Stage 1: Conceive
The first step of the lifecycle is for the customer to identify the need for the project, and brainstorm objectives and identify project stakeholders.
Once the project gets to AGDisplays, this stage involves gathering and defining the product requirements as defined by customer, company and/or applicable regulations. After specifications are placed, technical parameters are put together. Concept design is created. In the case of building LCD units and peripherals, drawings are gathered, and technical specifications are matched. This is the stage where LCD components are implemented to determine compatibility. The benefit of working with AGDisplays is that we are involved as much as you need us to be. We work from start to finish with your team to bring life to your vision. With over 40+ years of experience in handling, building and repairing displays, our design members are passionate about finding cost effective, compatible and safe components to bring your project to fruition.
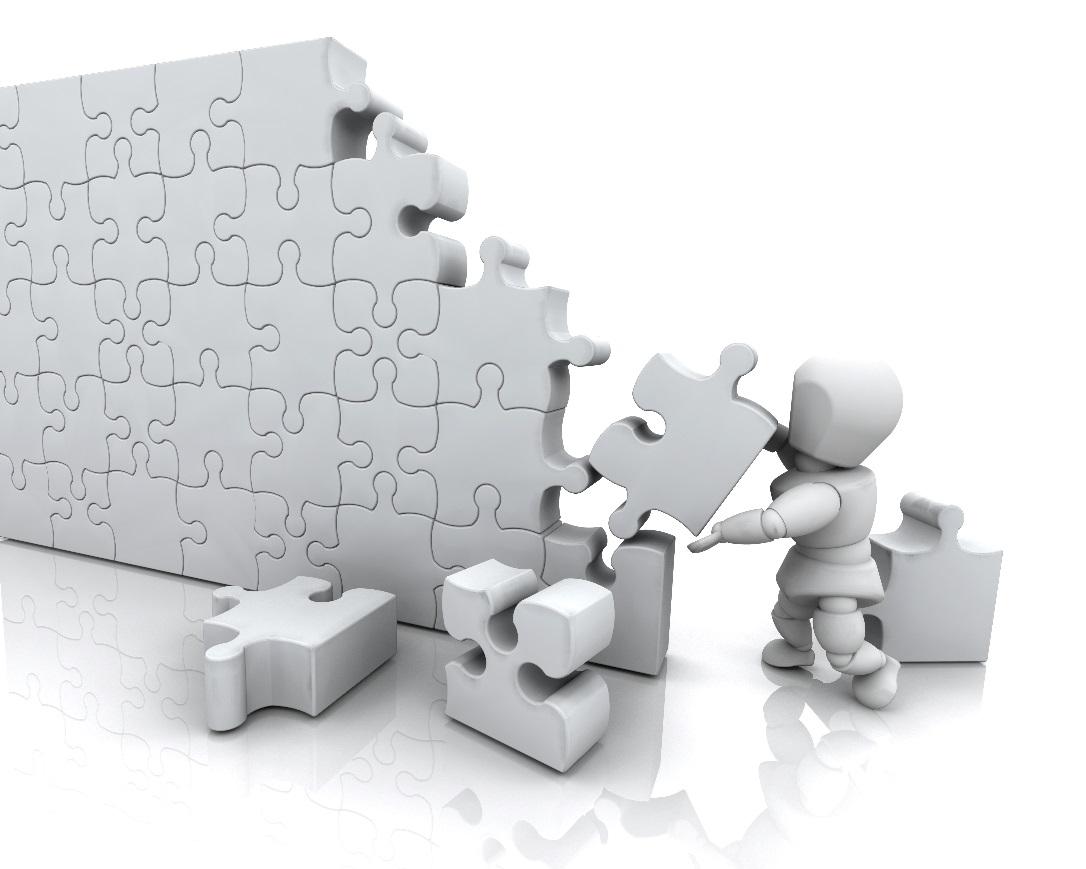
Stage 2: Design
Design and development takes place in this stage, and prototype testing can begin. This phase may involve CAD drawings, drawing specifications, specification definition, prototypes and creation of a bill of materials (BOM). If redesigns are necessary, prototype and design will be improved. All hands are on deck when teams work together to collaborate on electrical, mechanical, production, validation and logistical aspects of the project. Project supervisors, Stakeholders, or Managers use these elements to choose a definitive design to realize the final LCD product.
AGDisplays provides samples, development prototype kits and more upon request, to ensure your project is the exact specification required for your systems. Sample products are subject to various quality testing measures to ensure project specifics are met. Customers also get a sample in-hand by request. With product understanding, our design team finalizes the design of your project or suggests improvements, as necessary.
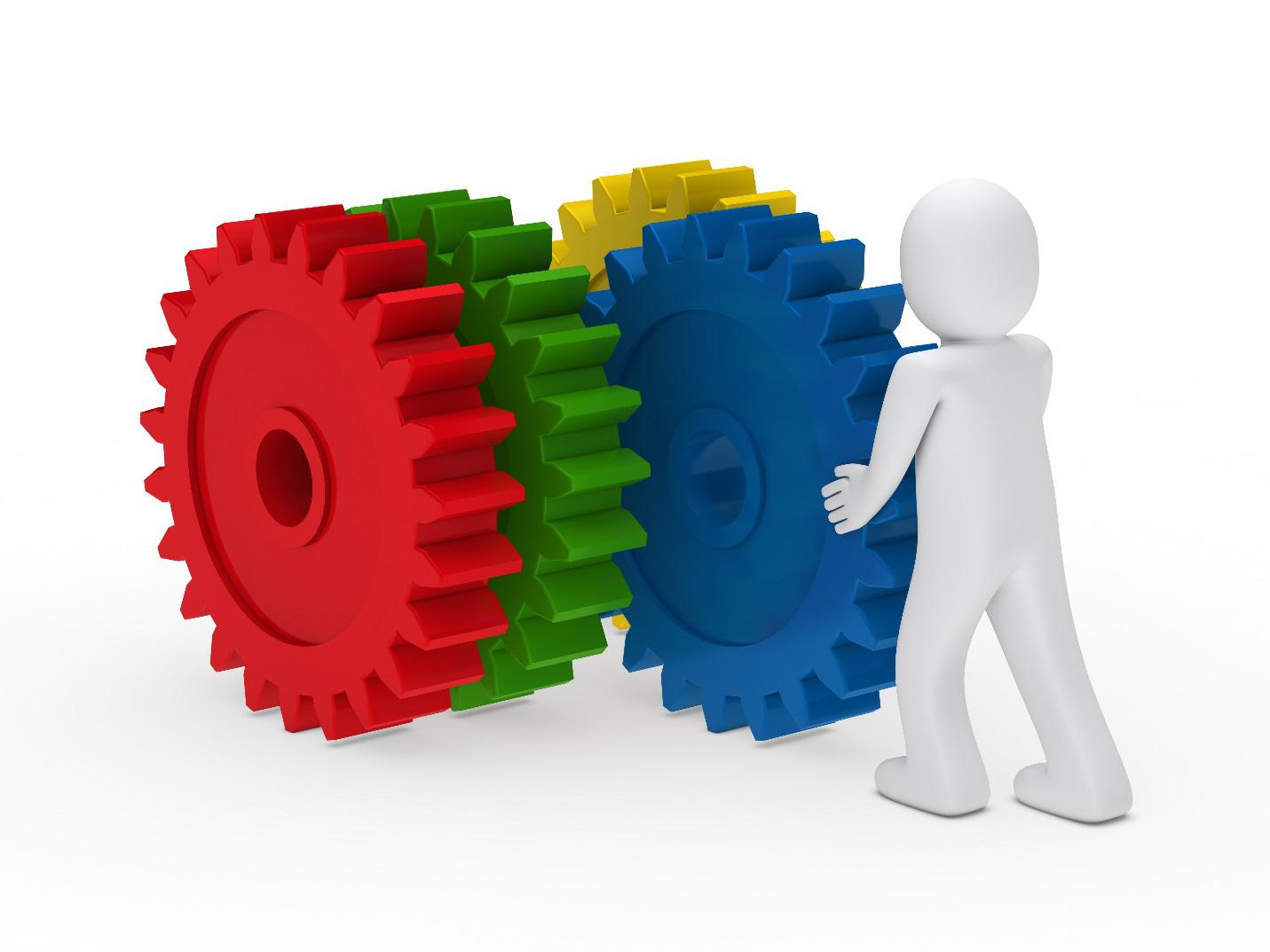
Stage 3: Realize
In this stage, preparing and executing the manufacturing and production takes place. Manufacturing methods are defined; potential suppliers or subcontractors may be brought in, a schedule is planned, materials and tools are ordered, instructions are given to personnel. The various moving parts of the Realize Phase are juggled by AGDisplays for your benefit. All design matters are cleared with stakeholders before production is begun.
Throughout this phase of the project, AGDisplays allows open communication between our teams and our customers. When either side has discussion points, we consider team communication an important part of any project management phase.
Inspections on deliverables are evaluated to ensure AGDisplays is only working with quality materials. During manufacturing, various product inspections take place such as performance measures. Employee performance is audited and in-between station workmanship is evaluated. At the completion of a product, final inspections are performed, and photo documentation is handled for traceability. Manufacturing performance is constantly overseen for any issues that may need to be addressed quickly.
Once products are manufactured and completed, quality tests are performed for specification verification and quality control. At the AGDisplays facility, we have in-house technicians who are meticulously trained to handle your display units with care. AGDisplays takes the hassle out of production scheduling and managing, providing your team with assurance that your deadlines are met with quality products that last.
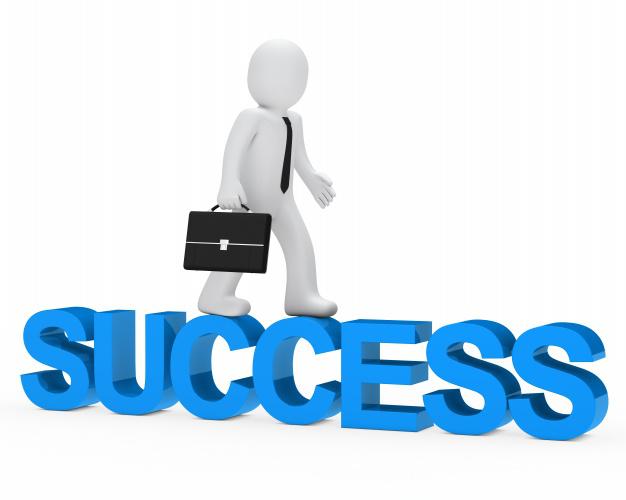
Stage 4: Service
This is the last stage of the product lifecycle. The ‘Service’ stage may include customer service and support, product servicing and disposal. At this stage is where the product eventually goes end-of-life. When creating a design involving advancing technology, it is always a smart idea to be mindful of product lifecycles.
EOL components prompt time and energy to be spent on re-designing of products and extra sourcing charges. LCD Lifecycle Support is a service for customers who have panels in need of component replacement parts. As broken components on your panel go EOL, AGDisplays quickly sources and installs components for increased panel lifespan.
We follow strict supply chain practices and well-maintained databases that lead to ultimate quality and customer satisfaction. Our International Procurement Office in China verifies these resources and quality of the companies we do business with; we have a secure list of trusted vendors with whom we maintain current business practices. Samples are always tested and verified before placing large orders. AGDisplays continues to watch the market for current LCD availability to stay on top of our customer’s needs. We also employ cross-verification methods for alternate components and sourcing.
If you or your company are buying an LCD direct from the LCD manufacturer, it is likely that you will eventually receive an end of life (EOL) notice about the panel(s) you have purchased. This EOL notice is there to let you know that the manufacturer will cease to produce that product part number in the coming years. If you are buying through a distributor, there’s a chance the EOL notification may not reach you. Purchasing the right LCD panel itself is a tedious task. Considering lifespan on top of that may add to the complications of selecting the right display.
Benefits:
- Improve your product quality and reliability
- Reduce time spent on manufacturing management
- Expand unit lifespan by utilizing repair and end of life services
- Maximize supply chain collaboration with AGD’s global outreach
- Improved forecasting
- Access to end of life panels and components
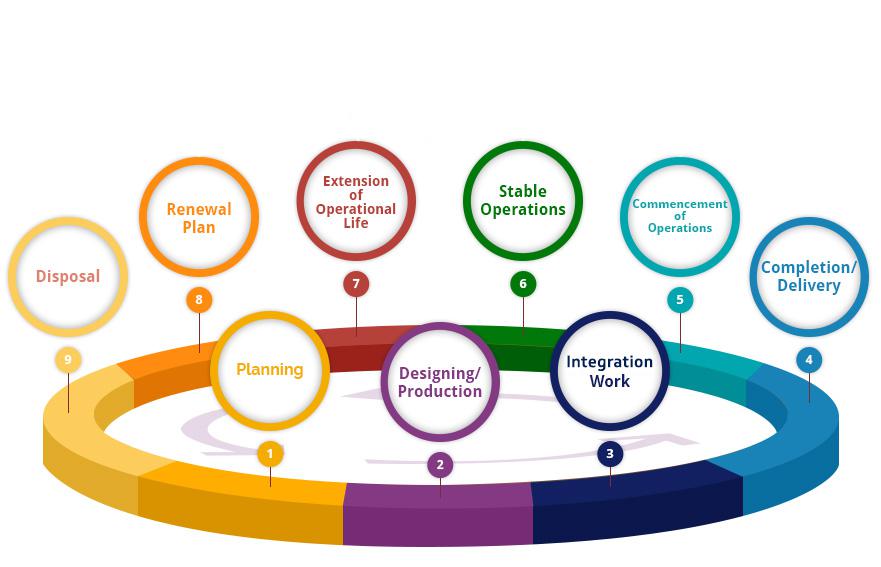